It's flat, discreet – and absolutely essential.
It's often the smallest components that have the biggest impact on process stability – and the flat gasket in a Camlock coupling is no exception. If you choose the wrong material, you risk leakage, contamination and an involuntary production stoppage.
In this article, we zoom in on one of the underrated heroes of the process plant and guide you through the most important considerations you should make when choosing your Camlock flat gasket.
A small component with a big impact
Camlock-couplings are widely used in the process industry, especially in food production and chemical handling, where they must be able to withstand high pressures. But the actual sealing point – the flat gasket – is often the first place to be challenged when the plant encounters chemicals and temperature fluctuations. Although the gasket is small and invisible in everyday use, it plays a crucial role in operational reliability. Chemical degradation typically starts quietly – a small crack, loss of elasticity or microscopic porosity. And suddenly it is no longer just a gasket that fails, but an entire process that is put at risk.

Chemical processes wear harder than you think
In daily operation, flat gaskets encounter everything from strong cleaning agents with high pH to acids, solvents and hot liquids. When the chemistry is complex and the cleaning protocol aggressive, it is important to match the gasket material to both the process media and the cleaning routine. It is not just about what runs through the pipe, but also what is rinsed through afterwards.
Which material is right for your process?
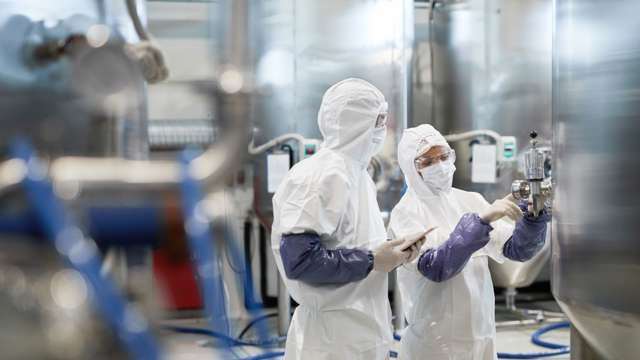
The choice of material is therefore not just about what can withstand the most, but about what matches your specific process, your media and your documentation requirements. That is why it makes sense to look at the entire process in context – from the temperature and composition of the media to cleaning routines and any approval requirements such as FDA or EU 1935/2004. A gasket that performs well in CIP cleaning with strong chemicals will not necessarily be the best choice in a fatty production at lower temperatures. The material must be suitable for both the medium and the environment, but also for the coupling in which it is installed. Although tightness is a given, operational stability and wear resistance are just as important – also in the long term.
We offer flat gaskets for Camlock in seven different material types and combinations, each tailored to different media and cleaning requirements in the process industry. Below is an overview of what each variant is suitable for.
-
NBR is a classic solution for oil-containing products and organic liquids. It has good resistance to grease and mineral oils and is well suited for non-aggressive environments. However, it has its limitations in contact with acids, bases and CIP cleaning with high pH.
-
EPDM, on the other hand, performs very well in alkaline environments. It is resistant to steam, hot water and strong cleaning agents, making it a good choice for food production where CIP systems are part of everyday life. However, it should be avoided where there is contact with oil or solvents.
-
Viton is a chemically resistant material that can withstand acids, solvents, CIP and high temperatures, making it ideal for demanding processes.
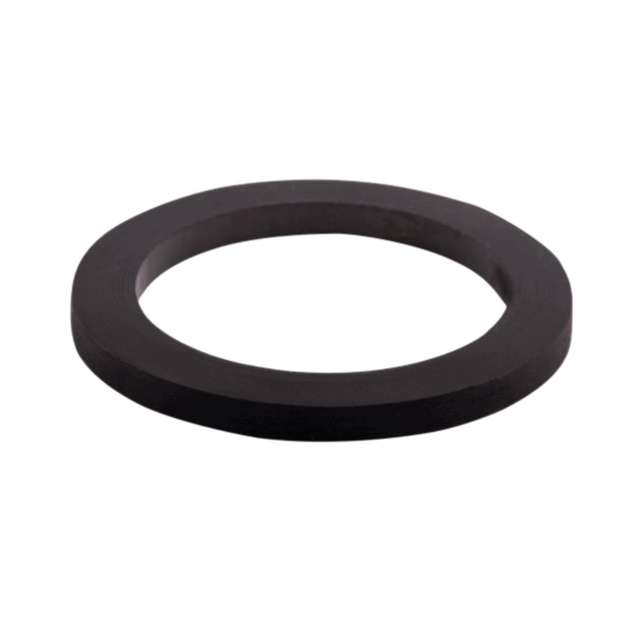
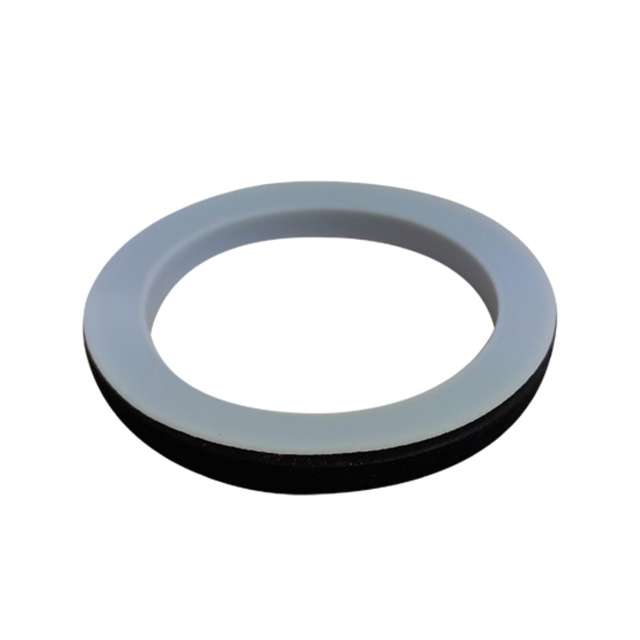
- PTFE/EPDM combines a chemically resistant contact surface (PTFE) with a flexible EPDM backing. This provides both tightness, dimensional stability and a high tolerance to aggressive media. It is suitable for environments where there are extra demands on both tightness and chemical stability – however, it is not suitable for CIP cleaning, as the combination cannot withstand repeated temperature and pressure fluctuations.
- NBR/FDA is a food-approved variant of nitrile rubber that combines the good properties of standard NBR with compliance with the requirements for materials in contact with food. This makes it suitable for oil-containing foods and non-CIP processes where documentation is important.
- EPDM/FDA covers the same type of applications as standard EPDM – but with full traceability and compliance with food legislation. It is typically used where there are both basic cleaning agents in connection with CIP and in environments with FDA approval requirements.
- Viton/FDA combines high chemical resistance and temperature tolerance with documentation in accordance with applicable food standards. It is an obvious choice in environments where chemicals, heat and traceability requirements play a central role.
The right gasket ensures smooth operation
Camlock couplings only become truly reliable when the flat gasket matches the process environment. With the right material, you extend service life, reduce the risk of leakage and ensure that your system can withstand chemical stress over time.
If you have any questions or need further guidance in selecting the most suitable flat gasket for your needs, our team is always transparent and ready to assist.
Contact us to discuss your process and together we will find the optimal solution for your specific needs via inquiry@alfotech.eu or +45 7020 0422.