In many cases, today's process plants can be complex in both structure and operation. Specialists on the floor as well as several types of technical components are almost always required to keep production running around the clock, for example in the food industry. The hoses form an extremely important part of the process plant's DNA and often their quality cannot stand alone in relation to having to avoid costly production stoppages. The bend radius is almost always just as important.
What is a bend radius?
A bend radius - or rather a minimum bend radius - refers to the minimum distance with which a process hose can be bent without damaging it or shortening its service life. At Alfotech, we distinguish between static and dynamic bending radii. In short, a static bend radius refers to an application where the bending of the process hose is not in motion. With a dynamic bend radius, it is just the opposite; here, there can be up to several repetitive movements per minute.
Example:
A food company contacts us with a request for the food-approved process hose Dynamic CLC, which is to be used for their new filling plant for yoghurt (see sketch). Their technical manager states that the process hose must be able to be bent 90 ° and that the model with an inside diameter of 38 mm is desired.
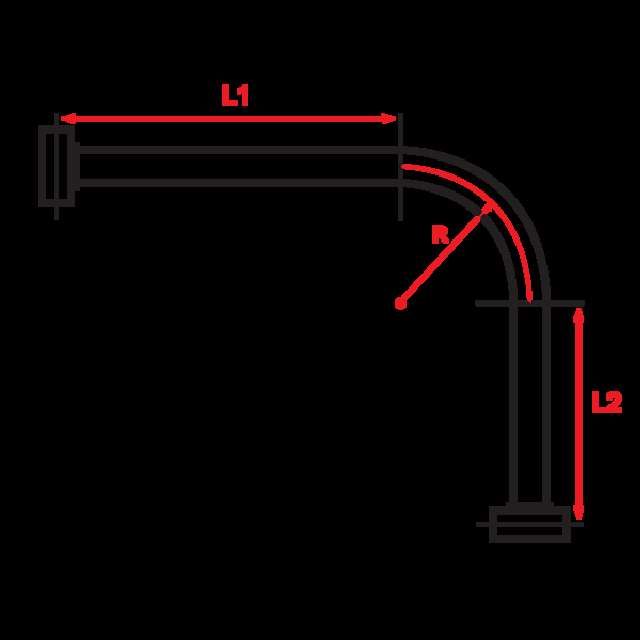
Based on the latter information, it appears from the product table on our website that the dynamic bend radius for this version of Dynamic CLC is 225 mm (R). From this we can calculate the minimum distance for the bend to 353.5 mm. On top of that we then put the necessary extra lengths that are not in bend (L1 and L2), including fittings.
Watch our latest video on Dynamic CLC
Dynamic CLC is a very flexible food-approved process hose.
Managing flexibility requirements is crucial
It is important to have flexibility requirements for the process hose identified in advance according to the production conditions. However, in addition to the bend radius, other significant factors must be considered, including relevant coupling types and sizes, operating temperature, and pressure, as well as other important factors in the production environment, for example issues in relation to torsion. If a repetitive bending of the process hose in operation is sharper than its design allows, both the process hose and its couplings are unnecessarily overstressed. In addition, a poorer flow of the medium occurs, leading to further complications. Ultimately, lack of flexibility in the hose solution can lead to an extremely costly production stoppage.
Our experienced sales consultants can advise you
Alfotech has more than three decades of experience in consulting on process hoses. Our experienced sales consultants are always ready to help you find the necessary flexibility requirements for your hose solution, making it as reliable as possible, regardless of whether it is for food, medicinal or chemical production. Contact us today by phone +45 7020 0422 or via e-mail inquiry@alfotech.eu.