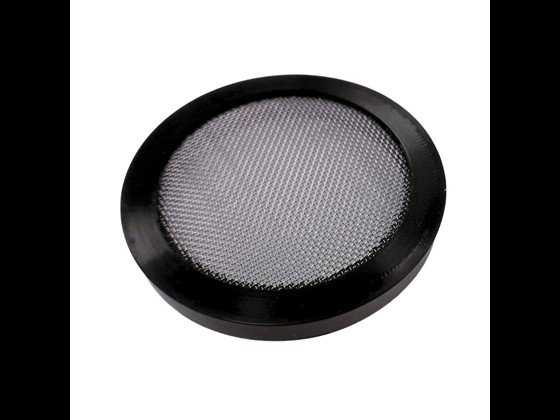
SMS union gasket with screen
AISI 316L (1.4404)
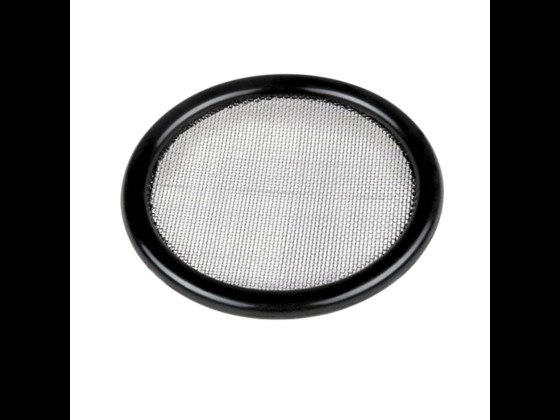
DIN union gasket with screen
Process plant filter, stainless steel, mesh certified.
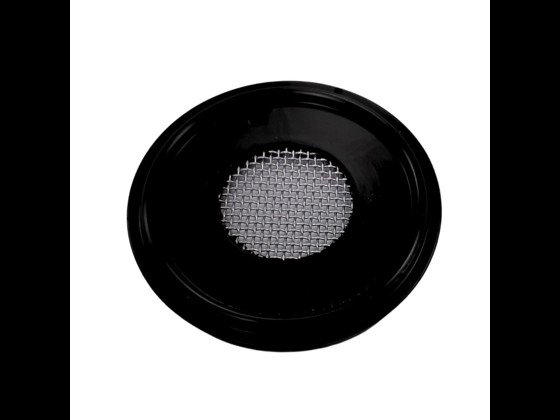
Clamp union gasket, ISO, with screen
Process plant filter, stainless steel, mesh-certified CLAMP.
Screen gaskets for protection of industrial equipment
Screen gaskets play a vital role as a component in different industrial equipment such as pumps, turbines, compressors and agitators. To prevent leaking fluid and the ingress of foreign bodies they can be used to seal important equipment. With proper screen gaskets you can prevent equipment issues leading to production downtime and a contaminated end-product.
When choosing the right screen gasket for the job, you must consider a few things. The type of media produced, temperature and pressure conditions, and the environment and safety are all important factors to consider. For example, in the chemical and pharmaceutical industries, corrosive and toxic production conditions may be encountered. And in the food industry, screen gaskets must be able to withstand CIP cleaning. It is also important to ensure that the gasket is compatible with the equipment and that it meets industry standards and regulations.
Screen gasket variants
Screen gaskets come in different variants, each suitable for different applications. The most common materials used for screen gaskets are rubber, silicone and PTFE.
At Alfotech, we have rubber screen gaskets available in different types such as Nitrile Butadiene Rubber (NBR), Ethylene Propylene Diene Monomer (EPDM), Fluorocarbon Rubber (FPM/FKM) and Polytetrafluoroethylene (PTFE). Silicone gaskets are known for their high temperature resistance and are often used in high-temperature applications. PTFE gaskets are highly resistant to chemicals and are often used in chemical processing applications.
Our screen gaskets come in standards such as DIN, SMS and ISO Clamp.
Main benefits of screen gaskets
Our quick guide to union gaskets with filter.
- Preventing the ingress of foreign bodies: small particles can travel through your process equipment during CIP cleaning or general cleaning. With properly installed screen gaskets you can prevent them from damaging your equipment and contaminating your end product.
- Preventing leaks: Screen gaskets help to prevent leakage of fluids or gases, which can cause equipment failure or environmental contamination.
- Maintaining performance: By preventing foreign bodies from entering equipment, screen gaskets can help to maintain its performance and prolong its lifespan.
- Reducing maintenance: By preventing leaks and improving efficiency, screen gaskets can help to reduce the need for maintenance and repairs, which can save time and money.
- Cost-effective solution: Screen gaskets are a cost-effective solution for preventing leaks, enhancing efficiency, and improving safety, as they are relatively inexpensive and easy to install.
Fastening methods and sizing
Screen gaskets are fastened in the same way as normal gaskets. ISO Clamp screen gaskets are secured with 2 flanges and a Clamp ring to create a tight seal and prevent leakage. SMS and DIN screen gaskets are placed on the gasket face between 2 flanges and secured by screwing on a union nut.
To prevent leakage, it's important to consider the gasket compression. Gasket compression refers to the amount of force applied to the gasket to create a seal. It is important to choose a gasket with the correct compression for the application to ensure a secure seal and prevent leakage.
It is also important to choose the right shape and size of screen gaskets to ensure a proper fit and secure seal. Accurate measurement of the equipment and knowledge of which foreign bodies to stop the ingress of, is acquired to have a correct match between gasket and equipment.
Installation and maintenance
Proper installation is also crucial for ensuring the longevity and efficiency of the equipment. When installing a screen gasket, it's important to ensure that the gasket is properly seated and that there are no air bubbles or wrinkles. This will ensure that the gasket provides a secure seal and prevents leakage.
Regular maintenance and inspection of screen gaskets is also important to ensure that they are in good working condition. This includes checking for signs of wear and tear and replacing gaskets when they become worn or damaged. In addition, the filter should be cleaned regularly to remove any particles, foreign bodies or unwanted objects that are stuck. Lack of cleaning can eventually lead to production stoppages and potentially damaged process equipment.
Choose a reputable supplier
It is important to choose a reputable supplier or manufacturer of screen gaskets, who can provide quality products and support throughout the entire process, from the selection of the right gasket to the installation and maintenance. At Alfotech, we have years of experience in providing, installing and maintenance of a wide range of different gaskets. We are always ready for a no-obligation chat and advice on which screen gaskets would best suit your operating situation.
Don’t hesitate to contact our professional team of consultants about your specific needs and criteria on +45 7020 0422 or by e-mail inquiry@alfotech.eu.